Cargill opens new advanced biodiesel plant in Belgium using BDI RepCat process
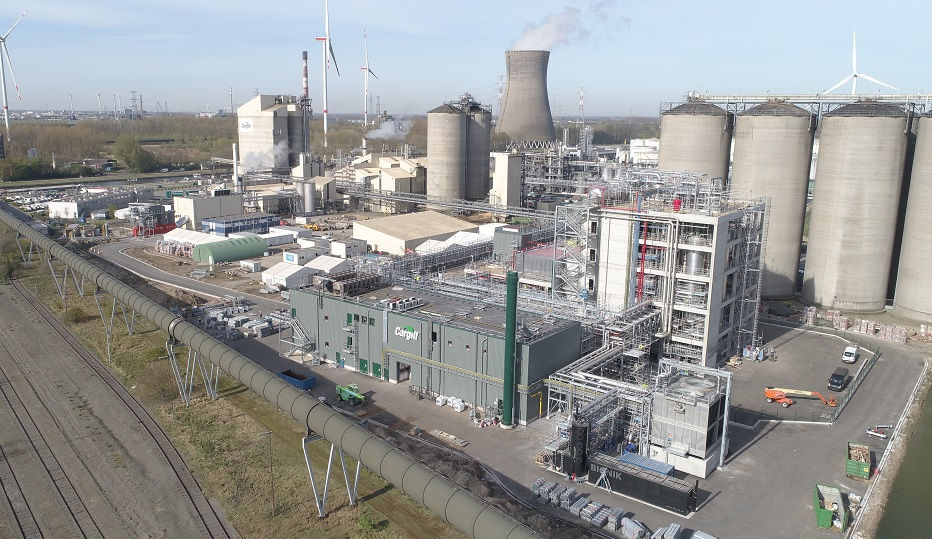
Cargill’s new waste-to-biodiesel production facility in Ghent, Belgium, is now operating. Under construction since late 2020, the $150 million project was designed and built by Austrian technology provider BDI-BioEnergy International utilizing its patented RepCat process.
The new Cargill facility is capable of manufacturing 35 million gallons per year (mgy) of advanced biodiesel from residual and waste materials. The RepCat process offers feedstock flexibility and employs a repeatable, or recyclable, catalyst. The industry-leading technology employed at Cargill’s new Ghent plant will be used to convert all types of liquid waste oils and fats—including used cooking oils, tallow and residues from edible oil production—into advanced biodiesel for the maritime and trucking sectors.
The Cargill project is noteworthy for several reasons. It is one of the largest waste-to-biofuel facilities in Europe. The project is also BDI’s largest assignment in the company’s 25-year history. And while Cargill has several biodiesel manufacturing facilities around the world, this new one is Cargill’s first such plant making biodiesel from waste materials and is co-located at its existing oilseed crush and Bioro biodiesel site in Ghent.
Cargill stated that its new waste-based biodiesel facility supports the circular economy, giving new purpose to products that previously were disposed of, or relegated to low-value applications.
“By leveraging advanced waste-processing technology, we are providing an innovative solution that meets global renewable energy demands, respects environmental needs and helps customers realize greenhouse gas commitments,” said Alexis Cazin, managing director for Cargill’s biodiesel and carbon divisions in Europe, the Middle East and Africa. “But the benefits are much broader, especially when considered alongside our global portfolio of alternative fuels, as they offer a bridge toward a future, decarbonized transportation system.”
The Cargill project in Belgium is the third RepCat plant built by BDI commissioned this year alone, with one in Hungary coming online in March, and another in California opening in April.
“Since day one of its existence, BDI has been committed to the research and development of ecofriendly technologies,” said Markus Dielacher, CEO of BDI-BioEnergy International. “Our involvement in this project represents the largest quantity of orders in the corporate history—the produced top-quality biodiesel is an essential contribution to a sustainable circular economy.”
Philippa Purser, president of Cargill’s agriculture supply-chain business in Europe, the Middle East and Africa, added, “Biofuels are one step in the journey, not the end goal itself. There is no single solution that will address the world’s current energy challenge. That’s why we continue to invest and support a range of solutions and will continue to innovate greener technologies.”