Celebrate National Biodiesel Day with a proven industry leader
- BDI-BioEnergy International GmbH
- Mar 17
- 3 min read
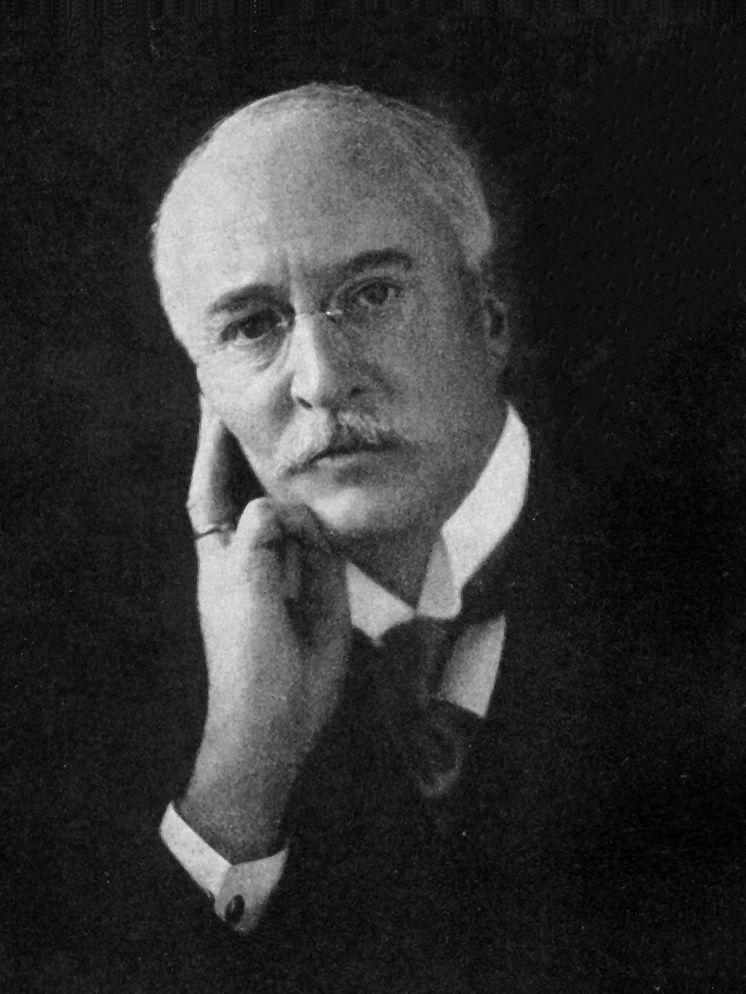
The United States celebrates National Biodiesel Day every year on March 18.
It is no accident this particular date was chosen.
It happens to be the birthday of Rudolf Diesel, the German inventor of the compression-ignition engine, pictured above.
Diesel developed his landmark engine in the 1890s, which debuted in 1900 at the World’s Fair in Paris where it ran on peanut oil.
The incredibly robust and efficient engine revolutionized society—125 years later, the diesel engine is the backbone of commerce as the powerhouse of choice for construction, agriculture, the transport of goods by sea, rail and over the road, and so much more.
Less than 100 years after the famed German inventor unveiled this engine that drove civilization’s progress, a small but resolute company was formed in nearby Austria that changed the course of fuel used in diesel engines.
This company spearheaded the modern movement to commercialize production of fuels suitable for the diesel engine that were made from waste materials such as used cooking oils and animal fats.
With March 18, being National Biodiesel Day, it’s the perfect time to take a closer look at a pioneering technology leader in the biodiesel industry: BDI-BioEnergy International.
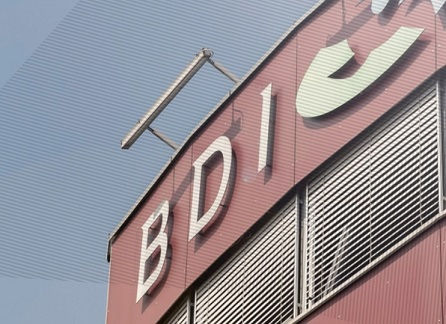
BDI was founded in 1996 in Austria, a country with a strong history of innovation in biodiesel, from groundbreaking research to the construction of the first commercial biodiesel production plant.
In this dynamic environment, BDI used its own in-house R&D center and research capabilities to develop technologies that are now implemented worldwide in the biofuels industry.
In fact, the company’s first contract in the U.S. was to design and build Griffin Industries’ biodiesel plant in Butler, Kentucky, for conversion of rendered products into biodiesel—more than 25 years ago!
Over time, the company’s competencies expanded to cover technology development, tailored process design as well as plant planning, construction and commissioning, in addition to after-sales customer service.
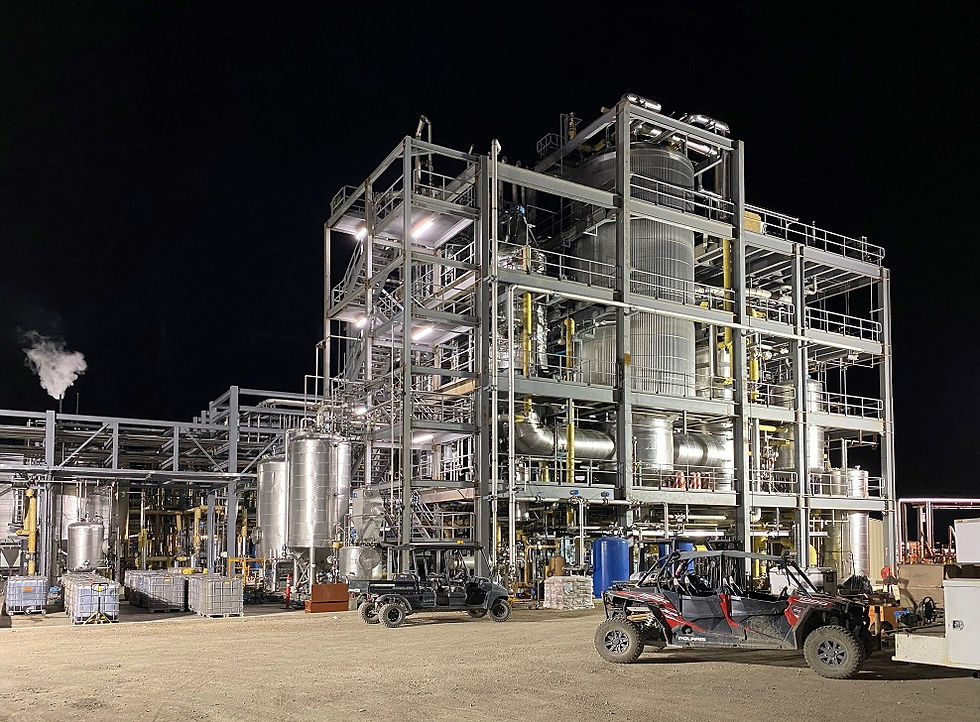
In 2022, with the commissioning of the first plants using BDI’s patented RepCAT® technology, including one in the U.S. (Crimson Renewable Energy), the boundaries of what biodiesel producers could use as feedstock were expanded.
The BDI RepCAT® technology, with its innovative reusable catalyst concept, is capable of handling feedstocks with up to 99 percent free fatty acid (FFA) content, meaning nearly all waste oils and fats can now serve as viable feedstocks.
This offers biodiesel producers unprecedented feedstock flexibility, allowing them to seek out cheaper options for a competitive edge in the market.

With the advent of renewable diesel and sustainable aviation fuel (SAF), one of BDI’s latest innovations is its Advanced PreTreatment technology, designed to efficiently and economically process waste oils for hydrogenated biofuel production.
The BDI Advanced PreTreatment process is modular, allowing it to be adapted to the requirements of raw materials, based on the core modules of prepurification, drying and adsorption.
Additional modules include polyethylene reduction via a special process patented by BDI, and the separation or conversion of free fatty acids from raw material.

These technologies are not limited to plants built by BDI alone—the portfolio has expanded to include the retrofitting of plants constructed by other manufacturers, ensuring that every biofuels producer has the opportunity to optimize their facility and improve its economic feasibility.
BDI’s RetroFit program supports customers from start to finish, beginning with an evaluation of the plant’s current state and progressing through engineering, delivery, construction and implementation of the optimization modules, and finally, commissioning of the improved process.
BDI now has over 70 industrial references worldwide and remains committed to researching and developing new technologies to advance the future of biofuels.