Different Technologies to Improve Biodiesel Quality
- Bárbara Sánchez González and Dario Altera
- Jun 27, 2024
- 4 min read

Production of high-quality biodiesel with low monoglyceride content is now possible with a new, elegant and economical process that can be easily integrated in existing and new biodiesel plants.
Biodiesel is a renewable biofuel that consists of fatty acid methyl esters and is typically produced by transesterification of vegetable oils or animal fats. Biodiesel (B100) has to meet minimum quality requirements that are specified in various international standards (EN 14214 and ASTM D6751). Some countries have their own national standards such as Indonesia (SNI 04-7182-2006) and Malaysia (MS 2008:2008).
Biodiesel quality parameters can be either feedstock or process dependent. Feedstock-related quality parameters such as iodine value or oxidative stability are intrinsic parameters related to the raw-material inputs and are generally not affected by the biodiesel production process.
Biodiesel Cold Stability
Cold stability is another critical quality parameter that can be notably influenced by a combination of factors, including feedstock-related parameters such as sterol-glucoside content and the degree of saturation measured by the iodine value. In practice, some of these quality parameters can be improved to a certain extent by the use of additives. For example, cold-flow improvers are added to improve the cold stability while antioxidants are added to get a better oxidative stability.
Process-related parameters such as ester content, degree of conversion (mono-, di- and triglyceride content) and total contamination result from the biodiesel production technology itself and can be improved by optimizing the process design and conditions.
One important parameter that determines the degree of conversion is the monoglyceride content. A high monoglyceride content contributes to poor cold-flow properties as monoglycerides tend to precipitate, causing problems in the engine’s performance.
Therefore, cold stability is an important biodiesel quality parameter as it will determine the maximum blending ratio of biodiesel in fossil diesel. Cold stability of biodiesel can be expressed by different parameters such as the cold filter plugging point (CFPP) or the cold soak filtration test (CSFT). Currently, 7 percent is the maximum biodiesel blend permitted in diesel fuel (B7) by the European Fuel Quality Directive (Directive 98/70/EC of the European Parliament and of the Council). This specific limit is established as higher blending ratios may result in clogging of fuel filters, especially in northern Europe and cold-weather conditions. This issue mainly arises from the poor cold stability that biodiesel with higher saturation exhibits, such as palm-based biodiesel. In countries with a (sub)tropical climate, such biodiesel can be used without any problem and even at higher blending ratios. Major palm oil-producing countries like Indonesia and Malaysia currently have biodiesel mandates of 30 percent (B30) and 10 percent (B10), respectively, and Indonesia is even considering increasing it further to B40.
Hence, in order to assure a better cold stability of (saturated) biodiesel, and given the increasing biodiesel-blending mandates, there is a trend by users and associations to implement more strict norms and quality control to avoid issues in the use of biodiesel. The European EN 14214 biodiesel standard reduced the maximum concentration of monoglycerides from 0.8 percent to 0.7 percent, while the American standard ASTM D6751 adopted a tight spec with a maximum of 0.4 percent monoglycerides for grade 1-B biodiesel. On the other hand, other countries like Indonesia, despite the higher blend, set an intermediate value of 0.55 percent for B30 blends.
How to Produce Biodiesel with Low Monoglyceride Content
Over the years, different technologies were developed to get a lower monoglyceride content in biodiesel by either pushing the conversion or removing them from the biodiesel.
Pushing the conversion during transesterification can be achieved by either dosing more catalyst and/or dosing more methanol. These conditions will give a biodiesel with lower monoglycerides with no yield loss but also with a higher operating cost. Nevertheless, due to the equilibrium of chemical reactions, there will always be a constraint on the extent to which monoglycerides can be reduced through transesterification.
Another option is to remove monoglycerides from the biodiesel. This can be achieved by distillation, which is a known process for the production of high-quality biodiesel. Less volatile components, including monoglycerides, di- and triglycerides, unsaponifiable matter and sterol glucosides, will remain in the distillation pitch, which will lead to a reduction in yield. The lower biodiesel yield together with the higher operating cost are seen as the main disadvantages of the distillation process.
Monoglycerides can also be removed from biodiesel by adsorption on specific silica-based or activated compounds. This adsorption process, however, is not widely used on an industrial scale due to a number of constraints.
Next to the different existing solutions to reduce monoglyceride content in biodiesel, Desmet developed a new, improved purification process that enables very-low residual monoglycerides at reduced capital investment.
Desmet currently offers a fully continuous biodiesel process with optimized transesterification conditions and low catalyst consumption. This process enables production of a final biodiesel product with 0.4 percent monoglyceride content, which covers the specifications of current European and other national biodiesel standards by a great margin.
To anticipate the biodiesel market evolution and meet the stricter demands on monoglycerides and higher blending mandates, Desmet has developed an improved biodiesel-purification process, which enables a further monoglyceride reduction to a final amount of below 0.3 percent. This process is applied downstream in the biodiesel process without increasing the catalyst consumption and can be integrated in existing and new biodiesel plants with minor adjustments, limiting the capital investments required in comparison to traditional distillation columns.
The improved biodiesel purification process is an integrated post-treatment, which involves contacting the biodiesel after the different transesterification steps with a concentrated alkaline solution. Very small dosages of concentrated solution are required, which make the process more cost efficient.
After contacting the biodiesel with the concentrated solution into a nano-cavitation unit, the mixture is sent to a specially designed reactor allowing variable mixing zones, enabling selective contact between monoglycerides and the chemicals, leaving the fatty acid methyl esters intact. As a result, a high-purity biodiesel is produced.
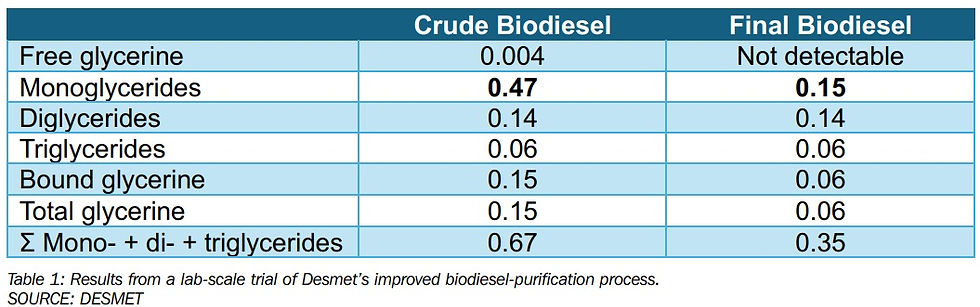
This patent-pending application has been deeply studied at laboratory scale, enabling a comprehensive understanding of the chemical interactions between the biodiesel components and the reactants (Table 1).

Additionally, the first industrial implementations have been successfully tested (Table 2) starting with variable monoglyceride content in crude biodiesel, allowing adaptation to different industrial-plant situations.

Authors:
Bárbara Sánchez González
R&D Engineer
Desmet
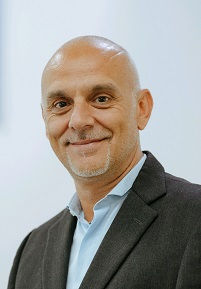
Dario Altera
Head of Oleochemicals &
Global Technology Manager-Oleochemicals
Desmet