Fast, Simple and Ready: Unlocking Opportunities in Coprocessing SAF
- Maria J. L. Perez and Milica Folic
- Jul 1, 2024
- 7 min read
Updated: Feb 13

Discover which units are the most suitable for coprocessing, what modifications are required and which feedstocks are best for SAF yield.
As the aviation industry seeks to reduce its carbon footprint, the production of sustainable aviation fuel (SAF) has gained significant attention. One proven technology, due to its relatively low capital and operating expenditures (capex/opex) and only modest complexity, is coprocessing renewable feedstocks in conventional refineries.
With the promise of an additional revenue stream, and usually simple diversification, refiners are asking what are the most suitable units for coprocessing? What modifications are required? And which feedstock is best for SAF yield? We have the answers.
Coprocessing Basics
In coprocessing, fossil feedstock (e.g., crude oil) can be partly replaced with renewable feedstock (HEFA-based) such as vegetable oil, animal fat or used-cooking oil. HEFA stands for hydroprocessed esters and fatty acids. Fossil and renewable feedstocks are processed together to produce renewable fuel. Coprocessing can be conducted in several hydroprocessing units within a refinery, such as a kerosene hydrotreater, diesel hydrotreater or hydrocracker—all three will be explored in detail later.
Measuring Coprocessed SAF
In the coprocessing approach, renewable and fossil feedstocks are processed together, resulting in a blended product. Physical segregation of the renewable component from the fossil component in the resulting fuel is not feasible. Sustainability characteristics of each fraction, however, are preserved in bookkeeping or mass-balance systems. These systems accurately track the amount and sustainability attributes of the renewable feedstock through the supply chain, ensuring that the renewable element and its benefits are accurately accounted for and credited.
Modifications for Coprocessing
Modifications required for a hydroprocessing unit to undertake coprocessing depend on its existing design and objectives. Several common areas may need to be addressed, however, including hydrogen availability, corrosion control, water formation and catalyst volumes.
Hydrogen availability is important as renewable feedstocks—due to their oxygen content—can consume significantly more hydrogen than fossil feedstocks (sometimes more than 31 times as much). Therefore, revamps of the make-up gas compressor and recycle-gas compressor may be needed to ensure sufficient hydrogen supply.
Renewable feedstocks can be highly acidic and may also contain chlorides (Cl), which can lead to Cl-induced corrosion. Depending on the point of injection of the renewable source, a material check may be required to assess potential acidity issues for corrosion control. The deposition of ammonium-chloride salts may also necessitate modifications in the point of injection of wash water at the reactor outlet.
Water formation also needs to be considered as triglyceride-based renewable feedstocks typically contain around 11 percent oxygen, which is converted into mostly water and small amounts of carbon monoxide (CO)/carbon dioxide (CO2) during hydroprocessing. This increased water formation may require adjustments to the water-boot capacity.
Coprocessing in Kerosene Hydrotreater
The kerosene hydrotreater is particularly advantageous for SAF production, especially in the European Union where carbon-14 measurements are required. This unit maximizes the SAF yield, ensuring that a larger proportion of the biogenic carbon in the renewable feedstock ends up in the jet-fuel fraction.

It is the quickest and simplest method to begin coprocessed SAF production as it can be implemented without significant alterations to existing units. This approach is both a low opex and capex solution, promising a short payback period. Additionally, it provides the flexibility to select the most suitable coprocessing starting point, allowing the inclusion of renewable feed up to 5 percent volume.
Using the high selectivity TK-930 D-wax™ catalyst in an existing kerosene hydrotreater will retain the highest possible biogenic carbon in the jet fuel and ensure that it meets the demanding freeze-point specifications. The renewable fraction in the product will comply with the most stringent fuel specifications for SAF.
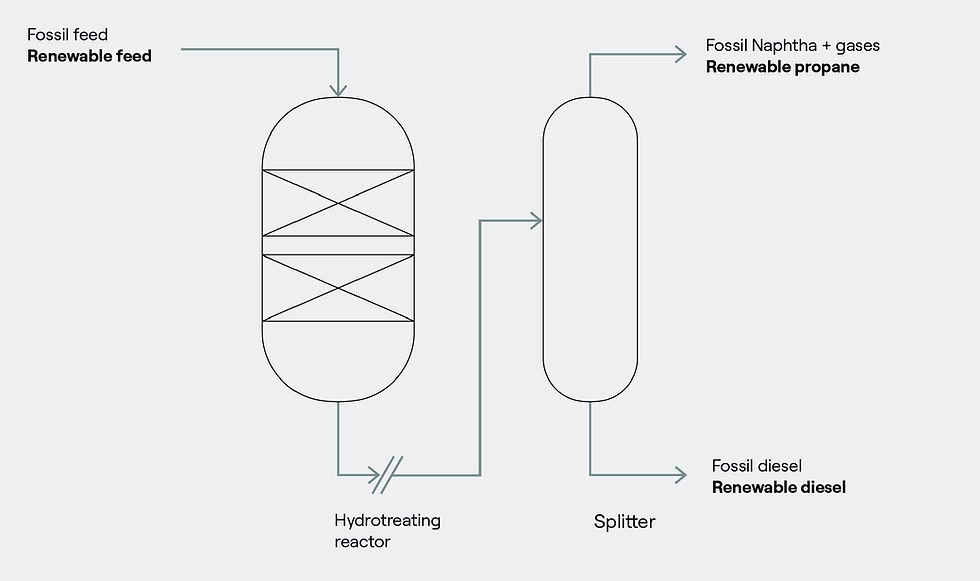
Coprocessing in Diesel Hydrotreater
Renewable feedstock can be introduced directly into an existing diesel hydrotreater together with fossil feed. The product will be a combination of renewable and fossil diesel. This method offers several benefits. Firstly, it typically requires limited or no revamp of the plant, making it a cost-effective option. Additionally, renewable grading and hydrodeoxygenation (HDO) catalysts can be swiftly incorporated, either by the next turnaround or even sooner through skimming processes. This approach boasts low opex and capex resulting, again, in a short payback timeframe.
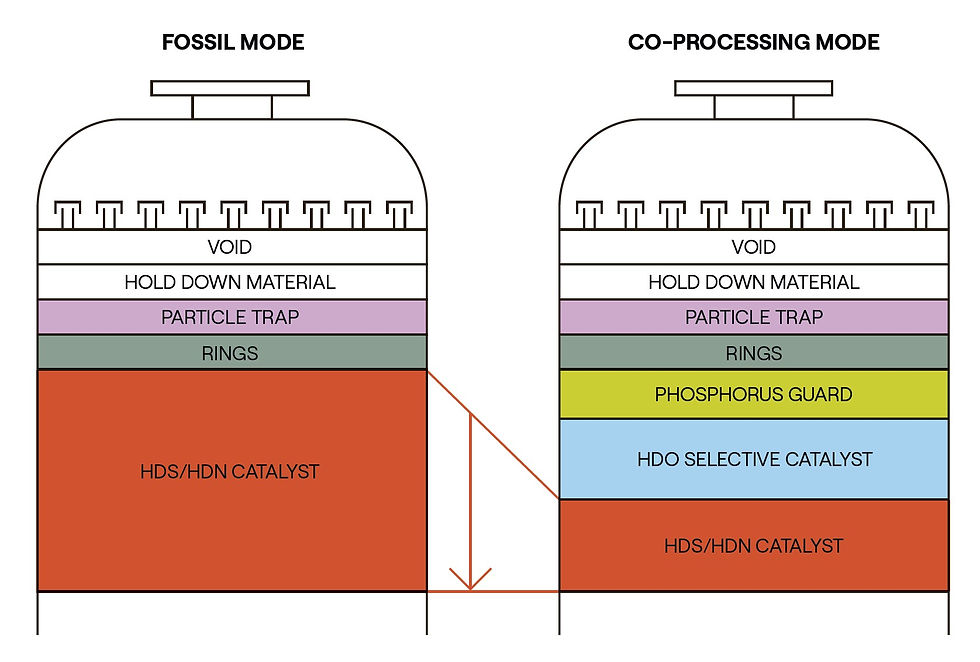
The implementation is straightforward, eliminating the need to wait for a fully renewable grassroots unit. Another advantage is the flexibility to determine the coprocessing starting point. Most notably, up to 10 volume percent of renewable feedstock can be seamlessly integrated with minimal equipment modifications. For coprocessing with more than 10 percent renewable feedstock, however, a revamp might be necessary. Nonetheless, this solution remains expedient and cost effective compared to establishing a new grassroots unit.
Coprocessing in Hydrocracking Unit
Hydrotreating units may be the primary choice so far for coprocessing renewable feedstock, but hydrocracking units should not be overlooked. Given their versatility, hydrocracking units are particularly suited for coprocessing renewables. We anticipate their usage will become indispensable in the future, particularly as the need to process more demanding second- and third-generation feedstock increases.
Unlike the hydrotreater, the hydrocracker offers significant process flexibility. It can be adjusted to accommodate specific feedstock availability and to produce the desired product. Coprocessing second-generation renewable feedstock like waste oils and fats, forest and food-crop waste and nonfood crops with vacuum gas oil (VGO) enables simultaneous production of various renewable fuels, including SAF, diesel and naphtha.
Which Unit Is Best?
The preferred hydroprocessing unit to coprocess renewables would depend on the configuration of the refinery, the specific constraints of each unit and the desired product.
Hydrocrackers offer some benefits due to their larger size and increased hydrogen availability, which allow for greater quantities and more flexible selection of feedstocks. While operational challenges exist due to high oxygen content in renewables, the impact on hydrogen consumption is less compared to hydrotreaters, mitigating operational difficulties.
Hydrocrackers handle contaminants more efficiently, as they are designed to process feedstocks with considerable amounts of contaminants like VGOs and heavy coker gas oil (HCGOs), minimizing the need for extensive catalyst replacement and ensuring uninterrupted operation.
If the target products are hydrotreated vegetable oil (HVO) or SAF, coprocessing renewable feedstock in a diesel or kerosene hydrotreater will retain the highest possible biogenic carbon in the diesel or jet fuel. If a combination of renewable products is desired, coprocessing in a hydrocracker is the preferred option.
Another possibility to produce SAF is using the fractionation system in the hydrocracker to cofractionate hydrotreated renewable diesel together with the fossil product. It is required to have hydrotreater renewable diesel available.
Catalyst Adjustment
Catalyst selection is crucial in producing efficient, high-quality coprocessed fuel. Topsoe’s catalyst selection for coprocessing, for instance, is designed to effectively address differences between renewable and conventional feedstocks, minimizing CO2 formation while optimizing cycle length, yields and coprocessing rates.
Additionally, Topsoe’s specialty guard materials and catalysts combat new contaminants introduced during renewable fuel conversion, such as phosphorus, potassium and sodium, ensuring profitable operation. Finally, dewaxing—vital for improving the cold-flow properties of biofuels like renewable diesel and SAF—is facilitated by Topsoe’s state-of-the-art dewaxing catalysts TK-930 D-wax™ and TK-920 D-wax™. These catalysts leverage selective isomerization to enhance cold-flow properties while minimizing yield loss to byproducts.
Optimal Operating Conditions
The operating conditions for coprocessing in a hydroprocessing unit can vary widely and are determined on a case-by-case basis. Several factors influence the optimal operating conditions, including the amount of renewable feedstock, product objectives, unit pressure, hydrogen-to-oil ratio, unit design temperature and temperature range of operation, and available catalyst volume or liquid hourly space velocity (LHSV).
Two key factors in this are obviously the desired product, whether it is SAF, renewable diesel or another product, and the volume of renewable feedstock to be coprocessed. These both dictate the operating conditions as higher volumes may require adjustments to the above-mentioned conditions.
To determine the optimal operating conditions for coprocessing in a given hydroprocessing unit, a thorough evaluation must be conducted. This tailored approach, which Topsoe provides to customers, ensures the most efficient and effective conversion of renewable feedstocks into the desired end products.
Impact of Feedstock Selection on SAF Yield
Finally, it is worth mentioning that the type of feedstock used in the production of SAF via coprocessing generally has a minimal impact on the yield. However, lighter feedstocks, particularly those with a higher proportion of carbon chains below C16, tend to maximize yields.
These lighter feedstocks often have a lower molecular weight and fewer impurities, making the coprocessing procedure more efficient and resulting in a higher yield of SAF. Nevertheless, the specific yield also depends on the other factors mentioned earlier, such as the operating conditions of the hydroprocessing unit.
Next Steps
Coprocessing renewable feedstocks in conventional refineries has emerged as a cost-effective and reliable technology to produce SAF and other renewable fuels. By understanding the suitable units for coprocessing, the necessary modifications, the optimal operating conditions and the impact of feedstock selection on the products yield, refiners can make informed decisions and drive the adoption of this production method, which is likely to be a key renewables pathway in the coming years.
Topsoe’s experience in coprocessing and in various SAF production pathways can be invaluable for customers entering coprocessing for the first time. A focus on proper evaluations and testing is obviously a key component in ascertaining how customer goals can be met. It also defines the optimal design of the production facility. When there are new, unique requirements, this is more important than ever.
But critically, when refiners are assessing new revenue streams, there needs to be constructive, forward-thinking dialog—this ensures that everyone is on top of the latest developments, the customer’s goals are always in sight and there is high transparency in terms of technology and design. The question, “If we change that, then how will that impact other factors?” is a recurring conversation, but one that makes sure aims are met. This open dialog also builds customer trust for the long term, where Topsoe becomes a value-driving partner and not a licensor making a one-off sale. You could say Topsoe is onboard with customers for the long haul.
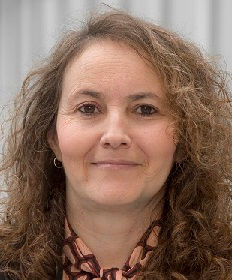
Authors:
Maria J. L. Perez
Senior Product Line Director for
Clean Fuels & Chemicals-Catalysts
Topsoe

Milica Folic
Product Line Director for
Clean Fuels & Chemicals-Technology
Topsoe