Feedstock Imperatives
- Christine Riedl
- Feb 27, 2023
- 5 min read
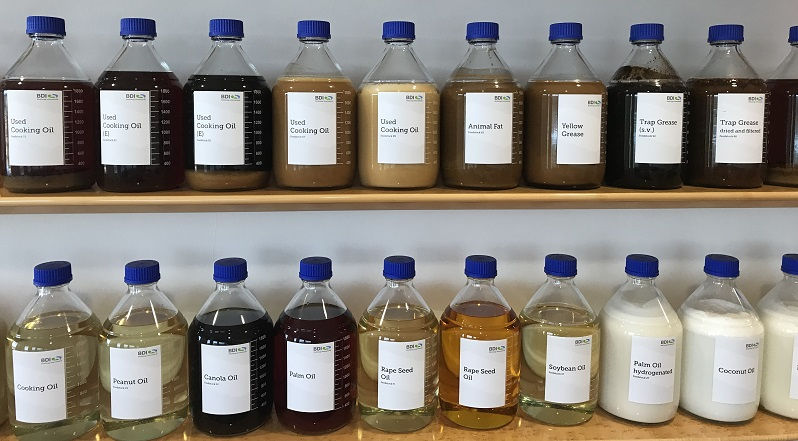
What biobased diesel producers need to know to develop a common-sense feedstock specification.
In the most relevant market newsletters, feedstocks like used cooking oil (UCO) or animal fats are specified by the free fatty acid (FFA) content, moisture, insoluble impurities and unsaponifiable matter (MIU), and sometimes sulfur. But is this information sufficient?
FFA content varies depending on the kind of feedstock. Refined vegetable oil usually has an FFA content of 0.1 mass percent (mass%) but can be as high as 0.5 mass%. In “good” UCO, the FFA content is at most 5 mass%, but there are qualities on the market where the FFA content is up to 15 mass%. In animal fats, FFA can range from 1 mass% up to 30 mass%. Even higher FFA content can be found in waste material like acid oils, which are generated, for example, in the soapstock-splitting process. The soapstock is obtained as a byproduct of the chemical neutralization of oils and fats. This soapstock can be split into fatty acids and water through acidification with a strong acid, such as the sulfuric variety. Other examples of high-FFA feedstock are brown grease, black grease and palm oil mill effluent (POME). These waste oils have an FFA content higher than 30 mass% and up to 90 mass%.
All of the feedstocks described above can be used for biofuels production, but depending on the technology installed, feedstock with the right FFA content must be chosen. The rule of thumb for using waste oils, however, is the higher the FFA content, the worse the rest of the feedstock quality parameters will be.
For example, UCO is a complex mixture of different substances formed during the deep-frying process. Water, introduced by the food during frying, leads to hydrolysis of the triglycerides to form mono- and diglycerides, as well as FFA as products of decomposition. As a weak nucleophile, water attacks the ester linkage of triacylglycerols. In addition, oxidation processes—preferably taking place at double bonds of the fatty-acid chains—lead to the formation of peroxides (primary oxidation products) by singlet oxygen oxidation in the first step. These peroxides will further react with fatty material to form all kinds of secondary oxidation products.
The complexity of oil degradation is increased furthermore by the fact that different types of oils behave differently regarding the rate of formation of polar components. In one study, a total of 220 compounds were identified as volatile composition products that formed during deep-fat frying, where a significant portion remains in the frying oil. These products show strong polar characteristics and can act as a surfactant, building a stable bond for free glycerol in biodiesel, which cannot be washed out during biodiesel purification. Thus, problems with too high a content of free glycerol and water can occur during UCO processing. Nevertheless, the UCO can be still used for biodiesel production, but there has to be the right pretreatment technology in place to ensure a stable operation.
Remember to follow the rule of thumb: The higher the FFA content, the worse the rest of the feedstock quality parameters will be. So, it becomes necessary to look in greater detail at which other parameters are crucial to know in order to select the right feedstock.

MIU
The next parameter specified in market newsletters is MIU. The acronym stands for three of the principal quality-control tests used to determine common contaminants in waste oils: moisture and volatiles, insoluble impurities, and unsaponifiable matter. For “good” UCO, the typical maximum value is 3 mass%. The more interesting part, however, is the ratio between these three components. Whether the water portion is 0.2 mass% or 2 mass%, for example, can determine if the raw material is suitable as feedstock for biodiesel or renewable diesel production. Therefore, this parameter also must be scrutinized more closely.
In general, higher water content is preferable as this means the amount of impurities and unsaponifiable matter is low. These are much more difficult to treat and have a greater influence on the production process. The water content can be reduced or handled by installing a drying unit, which typically can be designed for water content up to 5 mass%. But nevertheless, using a feedstock with higher water content will block the esterification and transesterification reactions and leads to greater consumption of chemicals and the creation of soaps, which ultimately leads to a lower yield. The other two parameters, however, are of more interest.
Some examples of insoluble impurities are solid-food residues in UCO and bone-meal residues in animal fats. When using feedstock with a high insoluble-impurities content to manufacture biofuels, there will be a significant risk of blockage in heat exchangers, pipes and other important equipment, which will lead to undesirable production interruptions. Therefore, these impurities must be pretreated up front before biofuel processing. This can be realized by means of filtration or centrifugation.
Unsaponifiable substances are compounds that cannot be converted into soaps by means of aqueous sodium-hydroxide solution and cannot be converted to biodiesel. Examples of these are sterols (e.g., cholesterol), fatty alcohols and mineral oils. For biodiesel producers, a high unsaponifiable content in feedstock will unavoidably lead to yield losses, production decreases, lower ester content in the final product and poor-quality glycerin—the byproduct of biodiesel production. So, in this small acronym there is a lot to know in order to make the right raw-material choice.
Sulfur
The next parameter to investigate is sulfur. In vegetable oil, sulfur is organically bound and therefore is also a component of UCO. For UCO, this parameter is not that critical unless the vegetable oil’s origin is from old rapeseed varieties, which have a high content of glucosinolates and means rapeseed rich in erucic acid. There are qualities on the market up to 30 parts per million (ppm) sulfur.
For animal fats, the rule of thumb is, the higher the sulfur content, the worse the rest of the feedstock quality parameters will be. Sulfur is an indicator for the degree of decomposition and can reach values up to or greater than 200 ppm. By using high sulfur-contaminated feedstock for biodiesel production, fat pretreatment is a necessary first step to reduce the water-soluble sulfur components. Other sulfur components can be reduced by means of biodiesel distillation to achieve the strict parameters of ASTM D6751 and EN14214.
Furthermore, sulfur poisons catalysts, which means high-sulfur feedstock is detrimental to the renewable diesel industry. And phosphorus is even worse than sulfur. Catalyst poisons are bound by the catalyst instead of the substance whose reaction it is supposed to accelerate. Thus, they block the adsorption capacity of the large surface area of the catalyst particles.
Coming back to the first question, “Is this information sufficient?”, here the answer is a clear “no.” There are many more parameters to know in order to avoid off-spec product on one hand and yield loss, production issues, and high costs for chemicals or catalysts on the other.

Plastics and More
One of these parameters, for example, is polyethylene-type plastics. Polyethylene in UCO is mainly in a solid state and exists in big particles, which means it is part of the insoluble impurities and can be reduced by filtration or centrifugation. In animal fats, the polyethylene is finely shredded or in molten form and, therefore, due to its similar density to the oil, elimination cannot be easily done by a simple filtration or centrifugation. If feedstock with a high polyethylene content is used in biofuel production, the producer can expect fouling issues in relevant process equipment, which ends up as decreased output capacity due to greater cleaning effort.
Being in the business of exploring waste oils and fats for more than 25 years, a high degree of know-how has been established and, thus, a number of additional parameters like alkalinity, phosphorous, polymerized triglycerides and many more have been detected. To ensure that the right feedstock is used with the appropriate technology, these parameters must be identified, established and understood. New frontend pretreatment technologies can be employed to render the feedstock suitable for the limits of a given biofuel production process, while backend quality-improvement units can help the final product meet the relevant industry specification. Contact us to learn more about feedstock parameters and their influence on different biofuel processes.

Author: Christine Riedl
Technical Sales Manager
BDI-BioEnergy International
+43 316 4009100