How Do We Maximize the Carbon Efficiency of Renewable Fuel Production?
Updated: Jun 21, 2022
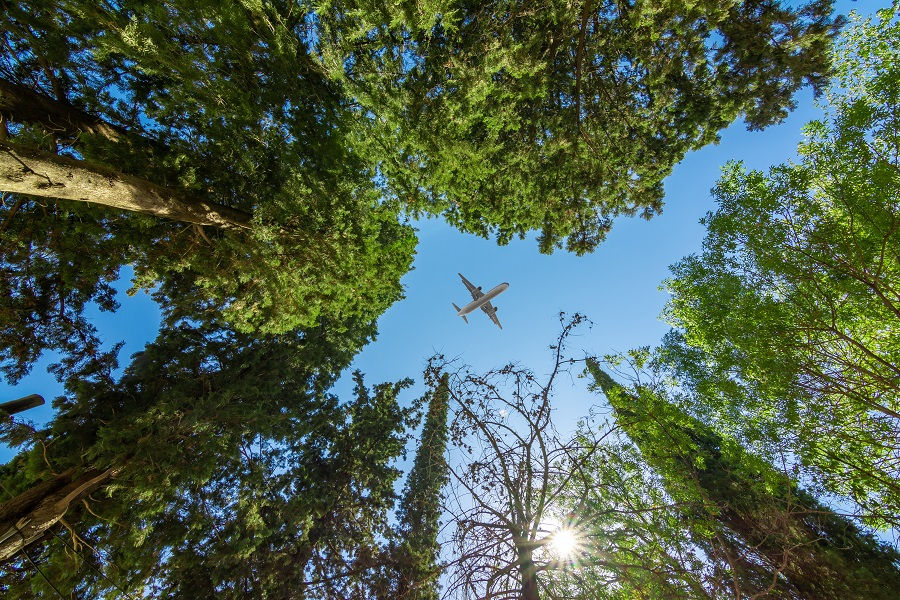
The use of Topsoe’s H2bridge™ technology is an effective solution for carbon-conscious, business-friendly renewable production.
U.S. renewable fuels production has been gaining momentum over the past few years. California, Washington, Oregon and New York all operate, or are preparing, subsidy programs for renewables, and there’s already a federal incentive for producers to adopt renewable production technologies. To maximize profitability and, by extension, viability, a renewable fuel business has to produce jet or diesel fuel at the lowest possible carbon-intensity (CI) score, thereby qualifying for greater subsidies overall. As such, it pays off—both short and long term—to minimize the CI of a renewable fuel throughout the value chain, including via the process technology utilized in production.
And one of the best ways to do that is by turning your fuel production’s main byproducts into renewable hydrogen with Topsoe’s market-ready H2bridge™ technology.
A Renewable Loop for Mutually Beneficial Production
During fuel production, the hydrotreatment of triglycerides in a Topsoe HydroFlex™ unit results in a small amount of off-gas, propane and naphtha. These are subsequently fed into the H2bridge™ unit, thereby reducing the operation’s total natural-gas requirement by 95 percent, and almost entirely eliminating the need for fossil-based natural gas as a key component of hydrogen production.
The green hydrogen produced by H2bridge™ is then sent to the HydroFlex™ unit, where it is used to hydrotreat and dewax the triglyceride products. Thus, Topsoe’s patent-pending integration of HydroFlex™ and H2bridge™ effectively reduces the CI of the renewable product by up to 10 points—a significant advantage for producers eager to secure the best possible profitability per barrel.
Redefining Hydrogen Efficiency with Legacy Technology
Efficiency is key to H2bridge™’s operation. A traditional hydrogen plant based on steam-methane reforming (SMR) produces significant export steam, resulting in a higher CI score. H2bridge™, however, generates only the steam needed for the unit itself, meaning that next to no energy is wasted as export steam—a characteristic that differentiates it from other hydrogen-production technologies.
The reason why H2bridge™ works as efficiently as it does is that the underlying Topsoe technology has existed for decades. The Haldor Topsoe Convection Reformer, which utilizes a single high-reliability burner, entered operation in 1992 and has since logged hundreds of operational years across 40 units around the world. Integrated within a renewable setup, it’s known as H2bridge™, producing hydrogen and steam at an 80/20 ratio, translating to 30 percent greater efficiency than a conventional SMR unit.
Maximizing Business Value While Minimizing Environmental Impact
All of this means good things for the environment. In addition to the biogenic nature of the already-reduced CO2 emissions resulting from use of the HydroFlex™ unit’s off-gases (as opposed to heavier fossil-driven CO2 emissions present in conventional fuel production), H2bridge™ provides its own significant benefits for renewable fuels producers. The solution enables full feedstock flexibility, all the way from C1 to naphtha, and since propane management is streamlined with H2bridge™, producers can reduce capital expenditures by eliminating the need for a depropanizer unit and propane storage tanks. With H2bridge™, our goal is to make renewable jet and diesel an easier, more profitable reality for our customers in the renewable industry. Our first H2bridge™ reference is already in operation, with several more at various stages of construction, and the completion of each helps another producer improve their competitiveness—and environmental impact—with a lower CI score.
Good business should, after all, be good for the planet as well.
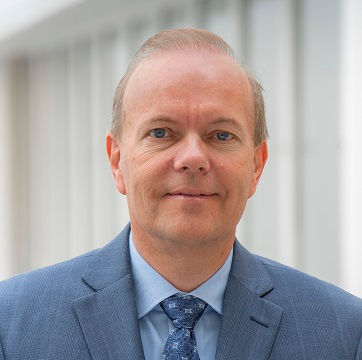
Author: Henrik Rasmussen
Managing Director for the Americas, Topsoe
281-228-5130