Raven SR, Emerging Fuels Technology partner on renewable diesel, SAF production technology
- Raven SR Inc.
- Oct 3, 2022
- 2 min read
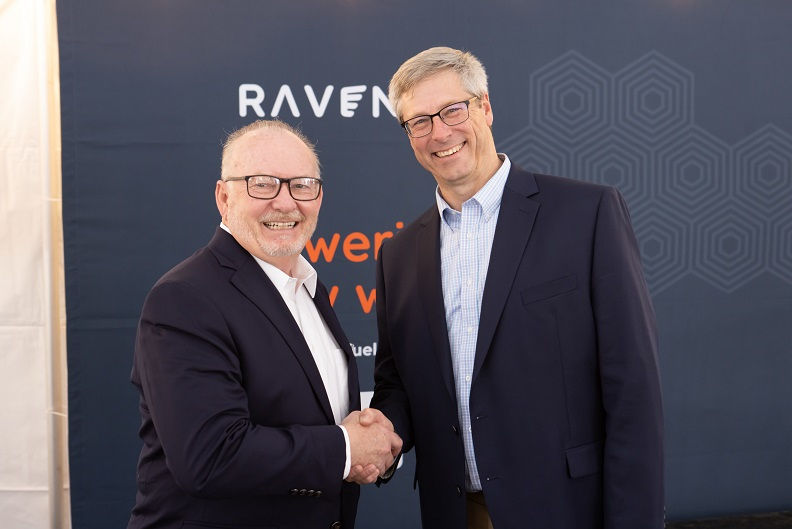
Wyoming-based Raven SR Inc. and Emerging Fuels Technology announced Sept. 29 that they have signed a memorandum of understanding (MOU) to integrate their respective technologies into an advanced system for producing sustainable aviation fuel (SAF) and renewable diesel.
The resulting production platform will include Raven SR’s patented steam/CO2 reformer process and EFT’s patented Fischer-Tropsch synthesis and Maxx Jet™/ Maxx Diesel™ upgrading technology.
This combination will allow Raven SR to produce high-quality synthetic fuels at higher-than-currently-feasible volumes within small, modular systems.
The Raven SR technology is a noncombustion-thermal process for converting organic waste and landfill gas to hydrogen and Fischer-Tropsch synfuels.
“We expect to go to market on an accelerated timeframe for SAF and other renewable Fischer-Tropsch fuels by incorporating EFT’s well-regarded catalyst/reactor technologies,” said Matt Murdock, CEO of Raven SR. “The collaboration with EFT, particularly their 75-barrel-per-day (bpd) and 500 bpd systems, which will match up well with our standard systems, will enable us to produce advanced fuels from waste on a local basis.”
Under the MOU, Raven SR and EFT will work together to optimize their process to maximize production while further reducing emissions.
The master license agreement will enable Raven SR to deploy its technology with EFT technology on a global scale, producing liquid fuels more quickly and nearer to market.
“This MOU represents a meeting of the minds and facilitates a means to produce premium synthetic Fischer-Tropsch fuels from waste materials,” said Kenneth Agee, founder and president of EFT. “We share similar ambitions of accelerating the production of renewable fuels with negative carbon intensity on a cost-competitive basis. We are very impressed with the first-rate quality of Raven SR’s syngas and the efficiency of its process.”
Raven SR’s technology is sufficiently flexible to provide an ideal source of syngas for Fischer-Tropsch technology. It is designed to produce more hydrogen per ton of waste than competing processes, according to Raven SR, making the cost per kilogram of hydrogen competitive, which has been a challenge of adopting hydrogen as a fuel source—and bringing long-term and integrated value to Raven.
The technology can also be implemented quickly, the company stated, meeting demand faster and closer to the market.
Raven SR’s unique process can also convert waste to produce other renewable-energy products, such as SAF, synthetic liquid fuels (diesel, Jet A, mil-spec, JP-8), additives and solvents (such as methanol, butanol, and naphtha).
“This collaboration with EFT provides Raven SR with the latest proprietary Fischer-Tropsch synthesis and Maxx Jet™/ Maxx Diesel™ upgrading technology to create a scalable, sustainable path for converting syngas into very high yields of high-quality jet fuel and diesel fuel products,” Raven SR stated.